Perfectly coated. Perfectly protected.
A good surface finish doesn’t just look appealing – it primarily protects a product from rust, scratches, and aggressive substances. This extends its lifespan and ensures reliable performance.
To maintain this protection over time, each surface layer must have the correct thickness.
A layer that’s too thin won’t offer sufficient protection, while one that’s too thick results in unnecessary material costs.
That’s why it’s essential in surface finishing to know how thick and even the coating is.
Regularly checking the coating thickness helps prevent issues and is a key part of effective quality assurance.
Thanks to QNix®, no coating can hide from you
No matter what your surface finishing requirements are – QNix® offers the right solution.
Whether you’re dealing with complex coating systems or working in tough production environments, our devices make your daily work easier.
When absolute precision and easy PC documentation are key, the QNix® 9500 is your perfect partner.
For those who prefer a straightforward approach without software, the QNix® 8500 remains a proven choice.
Which device is right for you? Find out now:
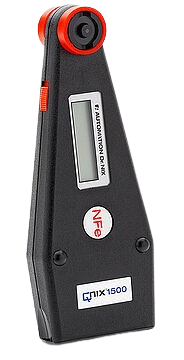
QNix® 1500
- Reliable and precise: Accurately measures even thin coatings on metal surfaces
- Perfect for small parts: Pencil probe ensures reliable results – even on edges and tiny components
- Simple and efficient: Memory slots for fast, repeatable measurements
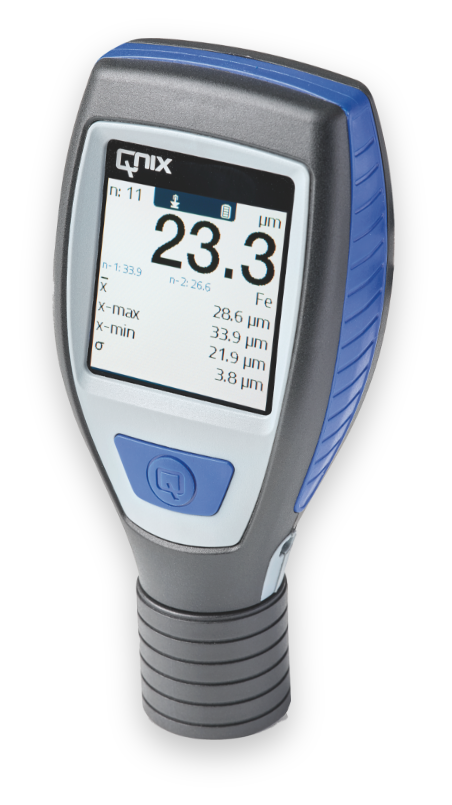
QNix® 5500
- Extremely durable: Protects against dust and splashing water – perfect for tough everyday use
- Fast and efficient: Quicker measurements thanks to automatic material detection
- Compact: Easy one-handed operation with a rotatable display
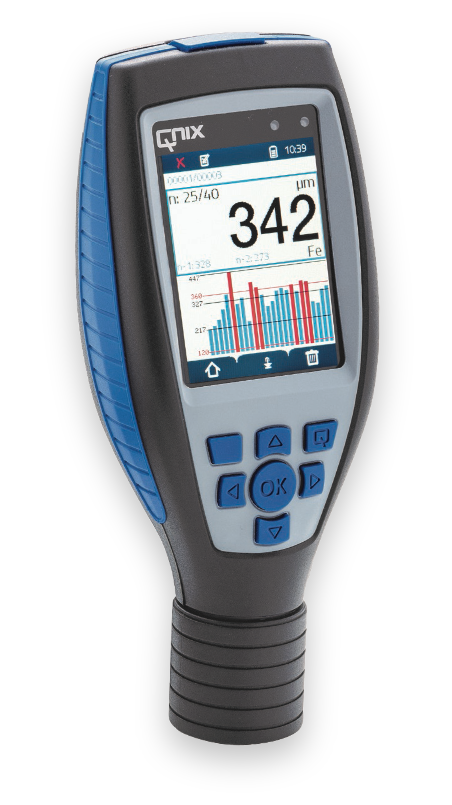
QNix® 9500
- Fast and precise: Also measures complex coating systems – ideal for demanding applications
- Flexible and easy to use: Modular design with interchangeable probes and user-friendly operation
- Perfect documentation: The integrated software lets you create custom reports and keep everything in view
Surface finishing for surfaces with added value.
Surface finishing is all around us in everyday life – often without us even noticing.
In industry, it ensures that metal parts not only look good but also function optimally and last longer.
In electroplating, ultra-thin layers of chrome, nickel, or zinc provide metal parts with extra protection against rust and wear.
With anodizing, aluminum parts gain a hard and durable surface that resists scratches and chemicals.
And with powder coating or painting, it’s not just about appearance: a properly applied layer can withstand even heavy use.
It reliably protects against environmental influences and ensures long-lasting, flawless product performance.
Each of these application areas has different requirements, but they all share one thing:
Quality depends on having the correct coating thickness.
Why coating thickness measurement matters
Your work deserves to be perfect. Every surface you coat should not only look good but also last.
And for that, the coating thickness has to be just right — otherwise, a good job can quickly turn into an expensive mistake.
Whether in the automotive industry, machinery components, or metal construction:
Only the correct layer protects against rust, scratches, and wear.
If the coating is too thin, the protection is missing.
If it’s too thick, it may crack or waste costly material.
Accurate measurement prevents all that.
With the right coating thickness, you avoid rework, keep costs under control — and deliver exactly the quality your customers expect. Every day. On every job.
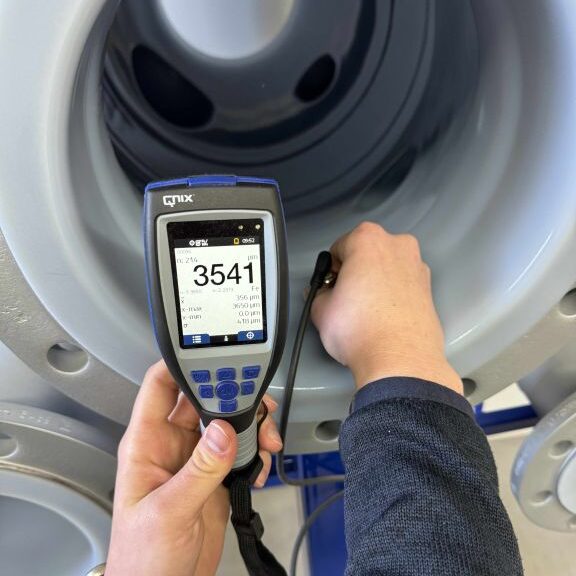
Standards and regulations – because quality work must be measurable
Anyone who applies coatings carefully wants to be sure the quality is right. Standards and regulations help with this. They ensure that coating thickness is measured correctly and that results are comparable everywhere—whether in electroplating, powder coating, or painting.
But what does this mean in practice? For example, there is DIN EN ISO 2178, which precisely specifies how to measure non-magnetic coatings—such as zinc, chrome, or paint—on steel. Or DIN EN ISO 2360, which defines how coatings on aluminum are tested. These standards ensure that every layer is exactly as thick as it should be—not too much, not too little. Because only then does it provide reliable protection.
With our coating thickness gauges like the QNix® 9500 and QNix® 8500, you measure precisely according to these standards. This way, you immediately know whether your coatings meet the requirements. And most importantly: whether your products are as good as your customers expect.
Would you like to learn more about our measuring devices for surface finishing?
Then get in touch with us – we’ll be happy to provide you with personal advice.
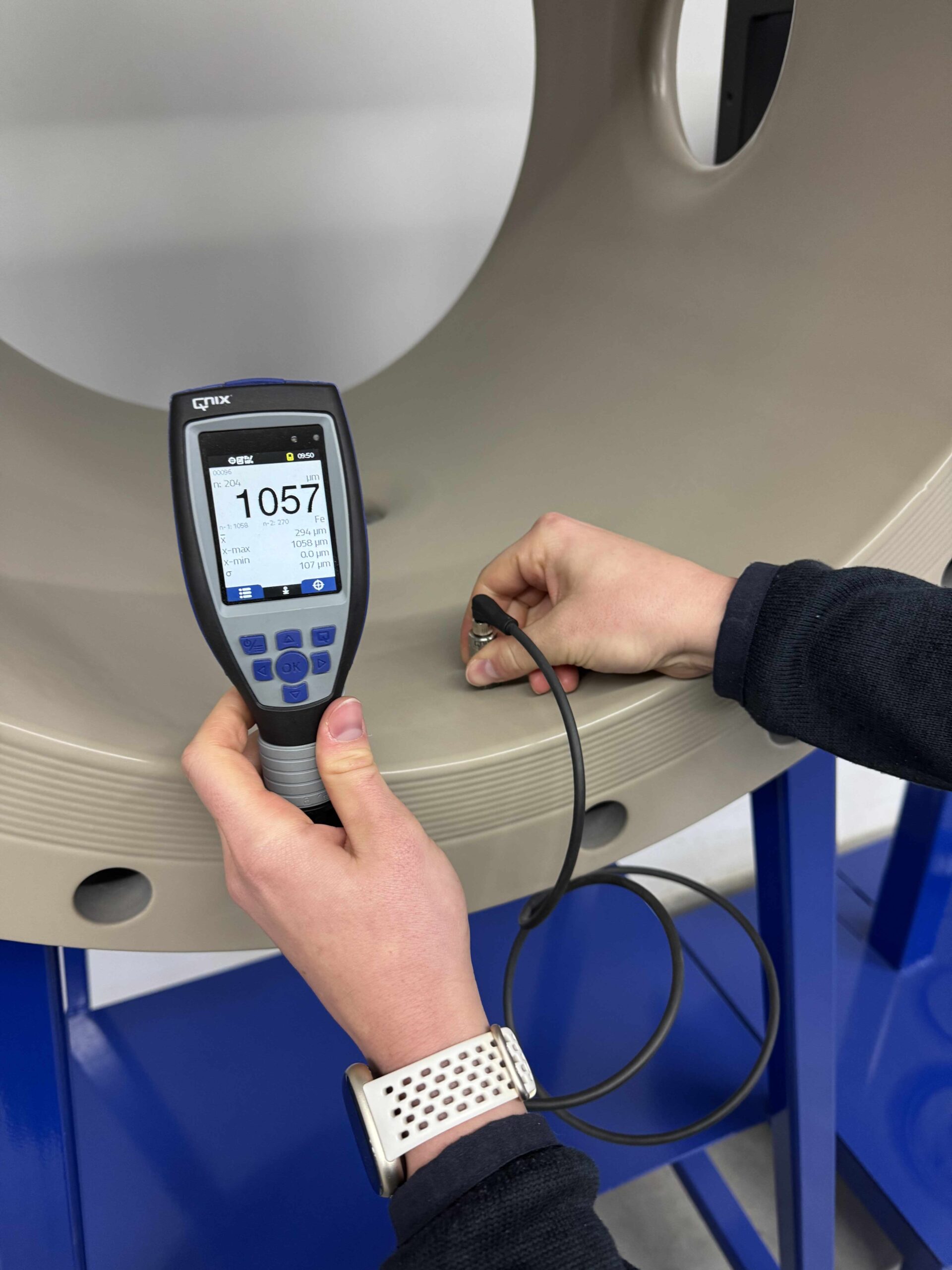
Challenges in Surface Finishing
Measuring thin layers precisely is often not that easy. The thinner a layer is, the more accurately you need to work in order to achieve truly reliable results. In addition, you often work with very different materials—from steel to aluminum or nickel. But not every material reacts the same way. Every surface brings its own challenges. What works on steel may not necessarily work on aluminum.
The shape and size of the parts also play a role: screws, bolts, or small workpieces with complex shapes often cannot be measured easily. In such cases, you need special solutions to achieve precise results even in difficult-to-reach areas.
In short: The more demanding the surface finishing process is, the more important it becomes to have fast, simple, and absolutely reliable measurements. That’s the only way to keep everything truly under control.
Answers to frequently asked questions
Which Measuring Instruments Are Suitable for Surface Finishing?
If you want to quickly and reliably know whether the coating thickness is correct, you need devices you can depend on. Our recommendation for surface finishing: the QNix® 9500 and the QNix® 8500. Both are easy to use and perfect for everyday work. Not sure which device is best suited to your requirements? We are happy to advise you. Use our contact form and we will get back to you promptly.
How Does Layer Thickness Affect the Quality of Surface Finishing?
The coating thickness determines how well a coating protects. Only when the thickness is just right will the surface withstand rust, scratches, and chemicals. If it’s too thin, protection is lacking. If it’s too thick, the coating can crack or come off. By checking the coating thickness, you ensure that the product lasts a long time and looks good.
Which Industries Are QNix® Coating Thickness Gauges Suitable For?
Our devices are used in many fields. This includes, for example, the metal industry—such as automotive manufacturing, railways, steel industry, mechanical engineering, shipbuilding, and aircraft construction. Our measuring devices are also in demand in the plastics and chemical industries. In electroplating, they are used for anodizing, chrome plating, or galvanizing. In addition, vehicle appraisers and paint shops (car dealerships, body shops, and experts) use our measuring devices. Maintenance and repair companies, as well as inspection organizations, also benefit from them. Finally, our devices are used in research and laboratory settings.
Why Is Coating Thickness Measurement So Important Here?
In surface finishing, the correct coating thickness determines the quality of the coating. If it is too thin, it does not provide sufficient protection against corrosion or wear. If it is too thick, unnecessary costs arise. Precise measurement ensures that the coating has exactly the right thickness. This saves material, prevents errors, and ensures that all requirements are reliably met.
Can I Get Help Choosing the Right Device?
Yes, we are happy to support you. Are you looking for a simple device for the automotive sector? Or do you need a solution for demanding tasks in surface finishing? We will help you find the right QNix® model.
Are QNix® devices waterproof?
They are not suitable for underwater measurements. However, our devices are very robust and withstand demanding environments, such as in corrosion protection or shipbuilding. In addition, they are protected against dust and splashing water according to IP64.
Can the device measure on plastic or other non-metallic materials?
No. For such materials, we recommend an ultrasonic measuring device, which we do not currently offer in our range.
Does the measuring device need to be calibrated regularly?
There is no legal requirement for calibration. However, we recommend an annual inspection at our facility to ensure accuracy and to issue an up-to-date calibration certificate.
Can the devices measure on different materials?
Yes, our devices measure steel, aluminum, copper, and zinc. They are designed to be precise and easy to use. As a rule, no calibration or probe change is required.
Is there training or support available for the devices?
Yes, we offer training so you can make full use of our measuring devices. If you have any questions or issues, our support team is always available to assist you.
Which probe is suitable for very small geometries and measuring surfaces?
The QNix® 9500 with a pencil probe and customized user calibration is ideal for narrow or hard-to-reach areas.
Does surface roughness affect the measurements?
Yes, you should take this into account. With a model from the QNix® 9500 series, you can compensate for roughness using user calibration. A mean zero adjustment will also provide more precise results in such cases.
What is the maximum surface temperature for coating thickness measurement devices?
Our devices cover a wide temperature range. They can be used at temperatures between -20 °C and +70 °C. Outside of this range, accuracy may decrease.
Does the accuracy vary depending on the measuring range?
No, the accuracy remains the same regardless of the measuring range. You can find the exact values in our technical specifications.
Get in touch with us.
We look forward to hearing from you.
Simply select the relevant topic and let us know how we can assist you. Our team will get in touch with you promptly and answer all your questions.
Your contact person
Metin Tek
Director Sales & Marketing
Head of Sales & Marketing
Tel: +49 221 91 74 55-23
Mobile: +49 160 92 75 69 97
E-Mail: m.tek@automation.de
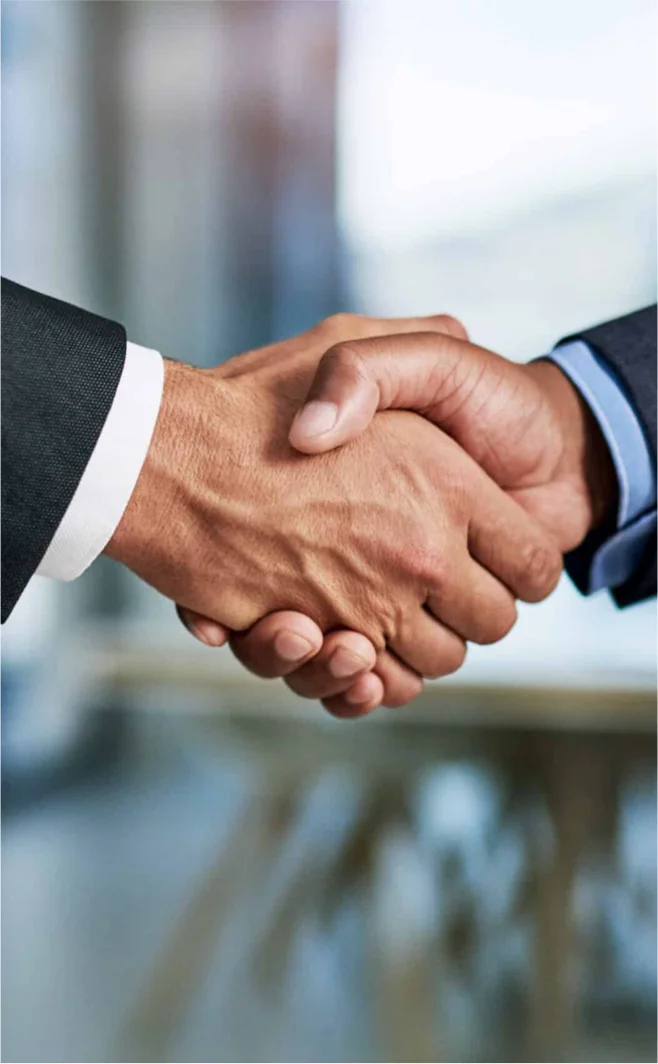